Modern Steel recently interviewed our very own General Manager, Mark King, to help construct the recently published article
"Above all, ART" that highlights the precise structural design and inspiring architecture of the Jan Shrem and Maria Manetti Shrem Museum of Art at the University of California, Davis. As a bender/roller, we were involved early enough in the process that we were able to reduce complicated curves, simplify the
steel bending and reduce significant costs. The
canopy consisted of HSS 14" x 10" rectangular tubing bent in
multiple planes (both the easy way and the hard way). An important highlight of the project was that some of the material that was bent in multiple planes was rotated off-axis by a slight amount, and the radius was large enough, that we were able to
bend it cold, which is a faster process than
hot bending.
[caption id="attachment_1091" align="aligncenter" width="1200"]
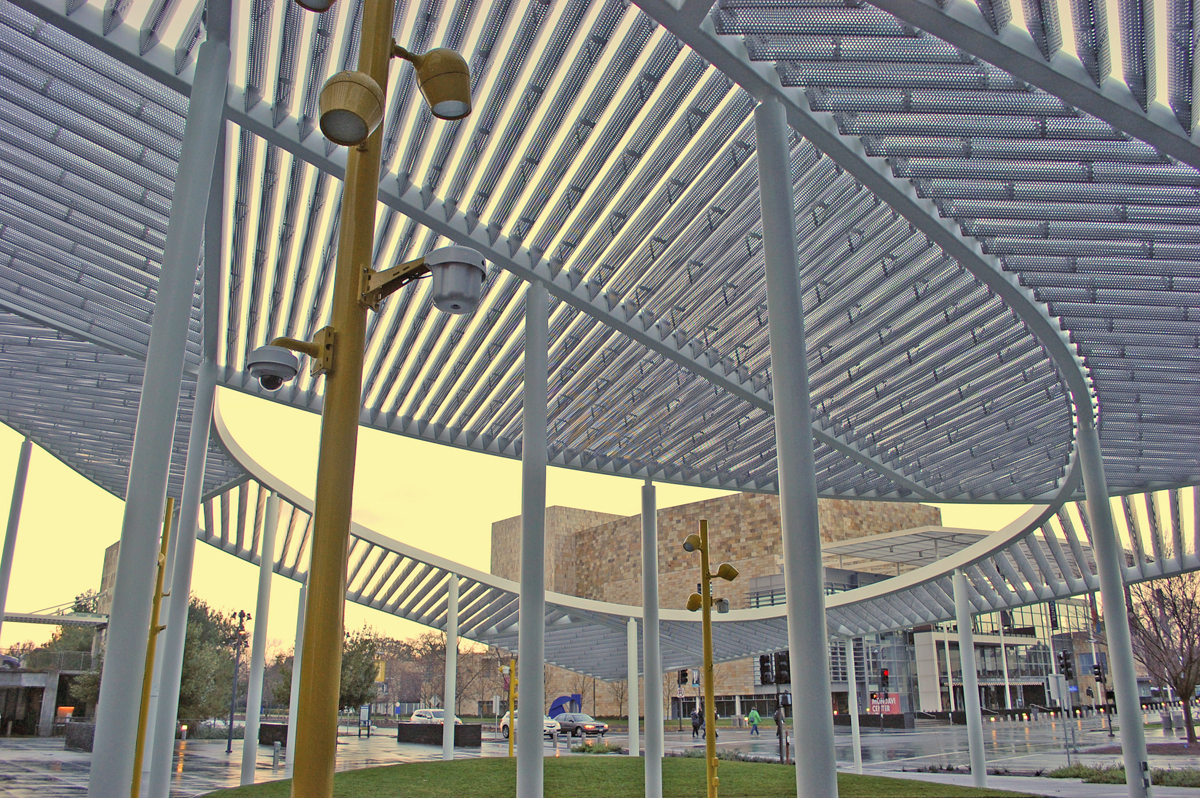
50,000 Square Foot Permeable Roof[/caption]
[caption id="attachment_1092" align="aligncenter" width="1200"]

Curved Steel Entry [/caption]
[caption id="attachment_1093" align="aligncenter" width="1200"]
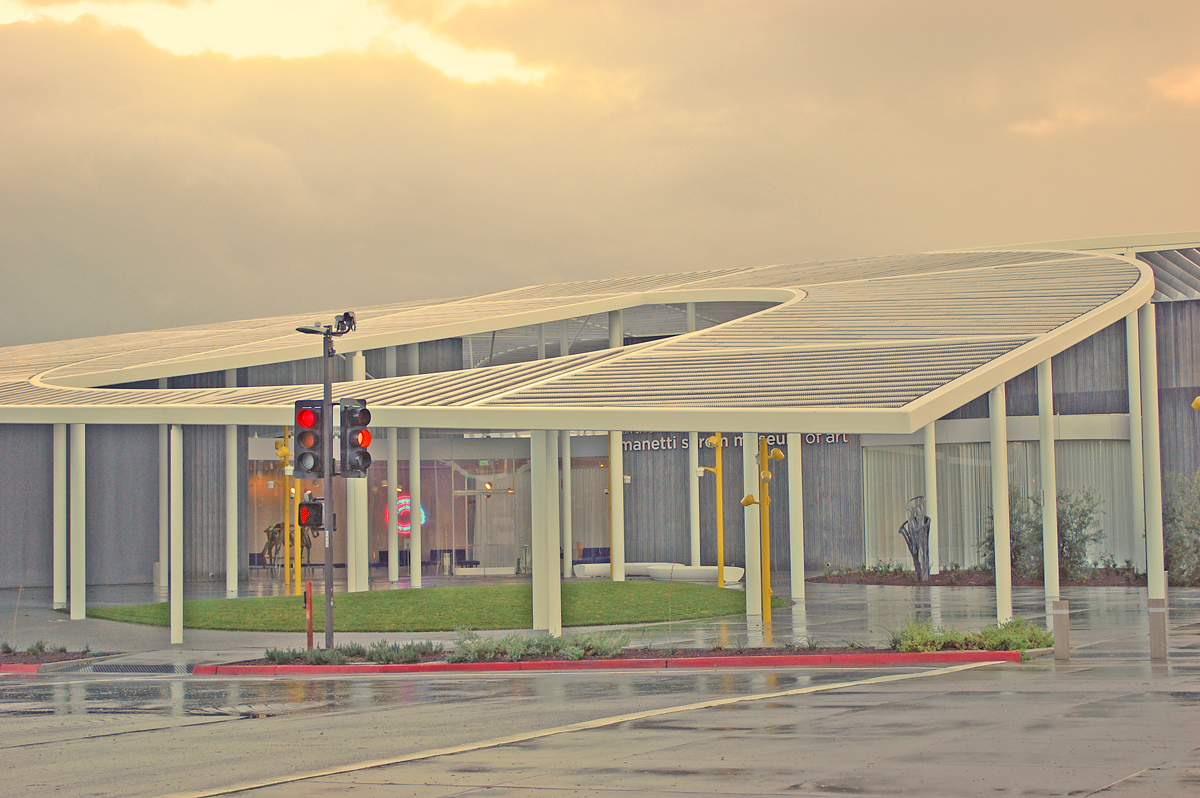
Overview of Curved Roof Structure[/caption]