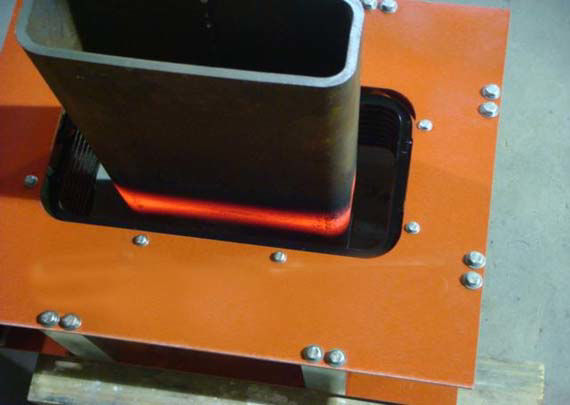
Induction Bending
AISC Design Guide 33 Curved Member Design Section 2.3.3
Induction bending is a hot-bending method that utilizes an electric induction coil to heat a narrow band—typically between 2 in. and 6 in.—around the member circumference to between 1,500°F and 1,950°F before it is curved by force. Equal wall thickness around the perimeter of the cross section is necessary for uniform heating throughout the section. As the member moves through an induction heating coil, it can be bent incrementally (similar to incremental step bending) but is usually rotated around a fixed-radius pivot arm. When a pivot-arm is used, a hydraulic ram pushes the straight section of the member through the coil at a constant rate (typically 1 to 2 in./min), with the leading end following the arc set by the pivot arm. After passing through the coil, the material adjacent to the heated section is usually sprayed with a coolant (usually water) or cooled with forced air, or the member is sometimes allowed to cool slowly in still air.
Although induction bending usually costs more than cold bending, there are several advantages that can make it the most appropriate bending method for some structural members. Because the inelastic bending strains are confined to the narrow heat band, small-radius bends are possible with high dimensional accuracy and low cross-sectional distortion. Induction bending may provide a viable method when the dimensional requirements cannot be met with cold bending. For example, induction bending may be the only method with the capability to bend a multi-sided hollow shape to a small R/D ratio with limited cross-sectional distortion. Because bending special shapes requires a significant investment in tooling, duplicate member quantities are required to make this method economically feasible. The induction bending process is inherently a form of heat treatment. With proper control of the essential variables, material properties can be enhanced by induction bending. Another potential advantage to induction bending is dimensional stability. A slight change in curvature can occur during lifting/handling, fabrication and erection. However, experiences indicate that induction-bent members are less susceptible to dimensional changes. This behavior is likely caused by the lower residual stresses compared to those induced during cold bending.