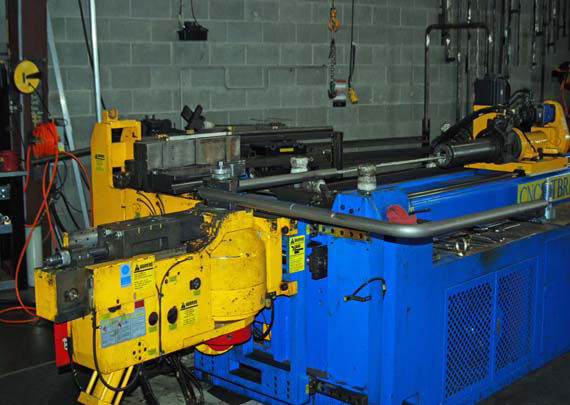
Rotary Draw & Compression Bending
AISC Design Guide 33 Curved Member Design Section 2.3.4
Rotary draw bending is a cold bending method where the member is clamped to a rotating bend die and drawn around the bend die. The tailing tangent is held against the bend die by a pressure die, and the bend die rotates until the desired geometry is formed. A mandrel is often placed inside the member to restrain cross-sectional distortion during the bending process. Bends can also be formed with special draw-bending equipment where deformations are controlled by tensioning along the member axis. Rotary draw bending is commonly used to form small radius bends in smaller-size round, square and rectangular HSS members. Specific tooling is required for each member size, shape and bend radius; therefore, this method is best suited for projects requiring many identical bends. This bending method is primarily used in the machine and parts industry (Weisenberger, 2016) and for piping (Riviezzi,1984). The maximum degree of bend is 180°, but the minimum bend radii of round HSS is approximately 50% smaller than that of other cold-bending methods (Riviezzi, 1984).