01 Oct 2013
Albina Provides Rolled Steel Canopy and Exceptional Customer Service for St. Jude's Hospital
Albina and Cundiff Steel Fabricating & Erecting provided 36,000# of TS 16" x 8" x .375" wall, TS 16" x 8" x .500" wall, TS 10" x 8" x .250" wall, and TS 16" x 16" x .375" wall all AESS for a canopy at St. Jude's Hospital. Cundiff Steel had the following comments about working with Albina: " I want to thank you guys for sticking with us on this project. It drug on for a long time and Aaron rebid it several times as we went through headache after headache with the engineers. I feel he went above and beyond to help us get this project on track. It took a lot of correspondence back & forth to get everything dialed in & Aaron was very helpful through all of it. The lead time from finally getting you approved drawings to us receiving the material was much less than we expected. Also, I appreciate the time Aaron took when I visited to show me the material and provide a tour of the facility to see how it all works. Thanks again for the great service." CHARLIE PISCOPO, V.P. Operations Mngr, Cundiff Steel Fabricating & Erecting
.
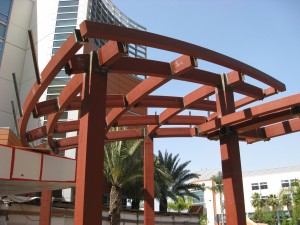